Noise has been a challenge since modern manufacturing emerged. Early on, neither trade unions nor companies knew just how dangerous noise was. Ignorance led to hearing loss for many industrial workers. And so it became clear that a better understanding and a solution to the problem was necessary.
It became apparent in the beginning of the 1970s that many people in industry were suffering from hearing loss. Accordingly, the labor market parties in Sweden set up a group tasked with investigating the problem and presenting a proposal on how to reduce noise. Acoustic engineer Stig Ingemansson was commissioned to lead the project.
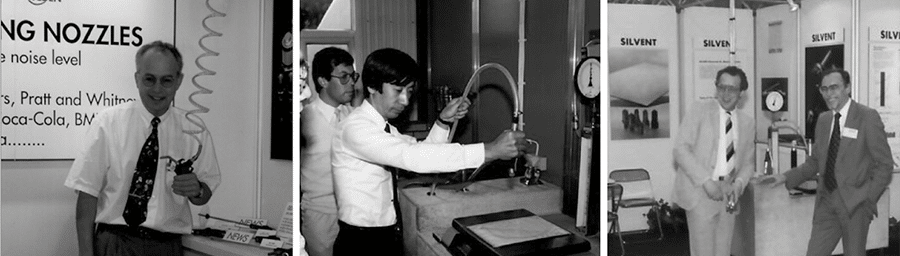
1976 – The beginning
To get more information on the problem, the project group began by conducting field studies and measurements in Swedish industry. It became apparent that almost every industry had noise problems, i.e. sound levels above 85 dB(A). Blowing with compressed air was one of the processes that generated the most noise. It was noted that many of the companies used ordinary copper pipes, aka open pipes, for cleaning, drying, cooling, transporting and sorting with compressed air. Or they used air blow guns based on the same principle, an open pipe. Following an analysis of other markets in Europe and the United States, the markets were also discovered to use the same method. The problem with blowing compressed air through open pipes is the increased air turbulence created as soon as the air leaves the pipe.
This results in very high, harmful sound levels. The project team understood they needed to develop a new solution if they were to reduce sound levels and hearing loss.